PROCESOS BASICOS DE FUNCIONAMIENTO
La soldadura por puntos es un método de soldadura por resistencia que se basa en presión y resistencia, en el que se calienta una parte de las piezas a soldar por corriente eléctrica a temperaturas próximas a la fusión y se ejerce una presión entre las mismas.
Generalmente se designa a la soldadura por chapas o laminas metálicas, aplicable normalmente entre 0,5mm y 3mm de espesor.
El soldeo por puntos es el mas común y simple de los procedimientos de soldadura por resistencia, los materiales bases se deben disponer solapados entre electrodos, que se encargan de aplicar secuencialmente la presión y la corriente correspondiente por ciclos produciendo uno o varios puntos de soldadura.
El principio de funcionamiento de este proceso consiste en hacer pasar una corriente eléctrica de gran intensidad a través de los metales que se van a unir. Como en la unión de los mismos la resistencia es mayor que en el resto de sus cuerpos, se genera el aumento de la temperatura en juntura, Efecto Joule
Donde:
Aprovechando esta energía y con una determinada presión se logra la unión. Solamente se obtienen soldaduras uniformes si las chapas a soldar están limpias, los óxidos superficiales son causa de variaciones en el tamaño y resistencia de los puntos de soldadura. Esto es especialmente cierto en el aluminio.
La presencia de óxidos o suciedad puede aumentar diez veces o mas la resistencia total entre los puntos de los electrodos.
La soldadura por resistencia es aplicable a casi todos los metales, excepto, zinc y plomo. Junto con la soldadura MIG/MAG son los dos procesos de soldadura en los cuales existe un mayor nivel de automatización robotizada.
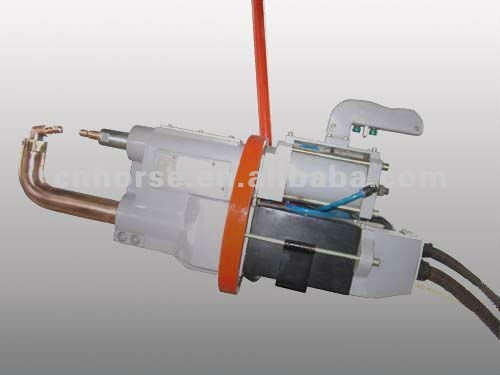
PARAMETROS :
- Intensidad - Tiempo soldadura.
- Resistencia eléctrica de la unión.
- Presion de apriete: Fuerza aplicada a los electrodos.
- Geometría de los electrodos.
INTENSIDAD - TIEMPO
La intensidad es el factor mas influyente en el calentamiento final (I^2). Resistencia constante. Tiempo en función intensidad.
- SOLDADURA RAPIDA: Mas intensidad menos tiempo.
- Peligro de fusión.
- Menos perdidas por conducción de calor.
- Apenas calentamiento de los electrodos.
- Soldadura de muy buena calidad y resistencia mecánica.
- Mas perdidas de calor y menos para la soldadura.
- Mas calentamiento de los electrodos.
- Soldaduras de escasa unión y resistencia mecánica.
- Intensidad máxima sin fusión.
- Regulación de tiempo de paso según espesor de chapas.
RESISTENCIA ELECTRICA DE LA UNION
- Es un parámetro a tener en cuenta pues influye directamente en la cantidad de calor generado en la soldadura.
- A mayor conductividad térmica menor resistencia al paso de la corriente. Aumento de intensidad.
- Resistencia total baja de 50 a 50 μΩ.
FACTORES QUE INFLUYEN EN LA RESISTENCIA ELECTRICA.
- La temperatura cuyo aumento provoca una disminución de la resistencia.
- La fuerza aplicada a los electrodos, que al aumentar la presión a las piezas a unir, provoca la disminución de las resistencias de contacto.
- El estado superficial de las superficies a unir. Su limpieza y la eliminación de rugosidades ocasionan menores resistencias de contacto.
- El estado de conservación de los electrodos, cuyo desgaste y deterioro provoca el aumento de las resistencias de contacto con las piezas metálicas a unir.
- Al inicio de la soldadura la presión debe de ser BAJA para resistencia de contacto elevada y calentamiento inicial con intensidad moderada.
- Esta presión debe ser SUFICIENTE para que las chapas a unir tengan un contacto adecuado y se acoplen entre si.
- Iniciada la "fusión" del punto, las resistencias de contacto es la zona delimitada por los electrodos. La presión debe de ser ALTA para expulsar los gases incluidos y llevar a cabo la forja del punto.
EXCESIVAMENTE BAJAS:
- Forja deficiente.
- Altas resistencias de contacto: Salpicaduras, Proyecciones, Cráteres y Pegaduras.
EXCESIVAMENTES ALTAS:
- Buena forja, pero si es excesiva puede provocar la expulsión del metal fundido. Disminución resistencia.
- Baja resistencia de contacto.
- Huellas profundas en las chapas.
- Partículas de cobre desprendidas.
- Deformaciones en los electrodos.
![]() |
PRESION RECOMENDADA PARA LA CHAPA DE ACERO: 10 Kg/mm2
|
- Sistema de puesta bajo presión de las piezas a unir.
- Transformador eléctrico generador de intensidad.
- Sistema de corte o temporización.
- Tensión de red estable.
- Presión de aire 6 bares.
- Alargadores de alimentación de suficiente sección.
- No forzar conexiones.
- Soplar con aire seco el interior de la maquina.
- No tirar de cables de conexión para mover la máquina.
FASES DE SOLDADURA POR PUNTO
Colocación de las chapas, es decir, de la pinza sobre las chapas.
TIEMPO DE BAJADA:
- Es el tiempo que transcurre desde que se inicia la operación de acercamiento de los electrodos hasta que comienza el paso de la corriente. En este tiempo se consiguen aproximar las chapas que se van a unir para obtener buena conductividad.
TIEMPO DE SOLDADURA:
- Es el tiempo durante el cual esta pasando la corriente eléctrica.
TIEMPO DE MANTENIMIENTO O FORJA:
- Es el transcurrido entre el corte de la corriente y el levantamiento de los electrodos. Enfriamiento con mantenimiento de presión: Grado resistencia.
TIEMPO DE ENFRIAMIENTO:
- Desaparece la presión y se separan los electrodos.
SECUENCIACION:
ELECTRODOS Y PORTAELECTRODOS: REQUISITOS
Requisitos:
- Buena conductividad eléctrica para evitar aumentos adicionales de temperatura.
- Tenacidad y alta resistencia mecánica a elevadas temperaturas.
- Buena conductividad térmica para que su refrigeración sea rápida y efectiva.
Geometría:
- Tronco - conicos:
- Angulo de la punta: 90º - 120º
- Diámetros de las puntas en relación con espesor chapas: 2e + 3 (mm) solo materiales férricos.
- Puntas casquetes semiesféricos o CAP:
- Radio de curvatura de la punta en función al espesor de chapas: 25e + 50 (mm).
MANTENIMIENTO:
- Es necesario el afilado para conservar la geometría y eliminar partículas y suciedad adherida.
ASPECTOS PARA EJECUCION:- Distancia entre puntos
- No es cierto que Aumenta la solidez del conjunto a multiplicar el numero de puntos y reducir el paso entre ellos.
- Efecto shunt:
- Excesivo consumo de energía.
- Soldadura de diferentes calidades.
- Distancia al borde o recubrimiento.
Distancia entre punto y borde de la pieza.
R= 2,5d
R= recubrimiento, d= diámetro de la punta.
Recubrimiento insuficiente:
- Expulsión de material fundido por la junta, debilitando la soldadura.
- Deformaciones en los bordes de las piezas, debido a la presión ejercida por los electrodos.
- deterioro de los electrodos que se ensucian con facilidad.
- Para no marcar en una pieza la forma de LENTEJA, intercalar una placa de cobre entre los puntos a soldar.
- La placa puede usarse como masa en muchas maquinas de soldadura.
Características mecánicas:
- Por su rotura.
Visual
- Soldadura por su color.
SOLDADURA DE DOBLE PUNTO
Se utiliza normalmente cuando no se tiene acceso con los electrodos a las dos caras de unión.
Para que la soldadura pueda efectuarse, el espesor de la chapa inferior ha de ser igual o mayor al de la chapa superior, evitando el cortocircuito a través de esta ultima.
DEFECTOS DE LA SOLDADURA
- Intensidad demasiado alta:
- Penetración demasiado profunda.
- Producción de salpicaduras.
- Intensidad demasiado bajo:
- Baja resistencia de la unión.
- Pegaduras.
- Presion de apriete demasidado alta:
- Marchas profundas en las chapas.
- Salpicaduras por expulsión del nucleo entre las chapas
- Presion de apriete demasiado baja:
- Salpicaduras.
- Agujeros.
- Deterioro de los electrodos por inclusiones de material.
- Tiempo de soldadura demasiado largo:
- Calentamiento excesivo de la chapa.
- Disminución de la calidad de punto.
- Tiempo de soldadura demasiado corto:
- Penetración demasiado pequeña.
- Pegaduras.
Muy buen articulo. Me gustaria saber si hay alguna manera de determinar el máximo diámetro de desgaste del electrodo que asegura una buena soldadura.
ResponderEliminarMe gustaria saber si tienes alguna referencia de tu articulo?
ResponderEliminar